Flexographic Printing Vs Other Methods
- Chapter I: A History of Flexo Printing
- Chapter II: Flexo Printing
- Chapter III: Litho Printing
- Chapter IV: Digital Printing
- Chapter V: Gravure Printing
- Chapter VI: Offset Printing
- Chapter VII: Screen Printing
- Chapter VIII: Corrugated Printing Considerations
- Chapter IX: Flexo Hybrid Presses
- Chapter X: Ready to Get Started?
A History of Flexo Printing
The basic process of flexography dates back to the late 19th century. It was not nearly as refined, precise, or versatile as the flexo process today, and can be best described as a high-tech method of rubber stamping.
Printing capabilities were limited to very basic materials and designs, with other printing methods greatly outshining flexo.
Over the past few decades, flexo technology has continuously evolved. This is largely thanks to the integration of Direct Laser Engraving technology, advancements in image carrier materials, and in press technologies. These innovations, among others, have led to increased quality and precision in flexo products.
These technological improvements have positioned flexography at the helm of consumer product and flexible packaging printing. Flexo is growing in popularity in a variety of other industries, too, including medical and pharmaceutical; school, home, and office products; and even publishing.
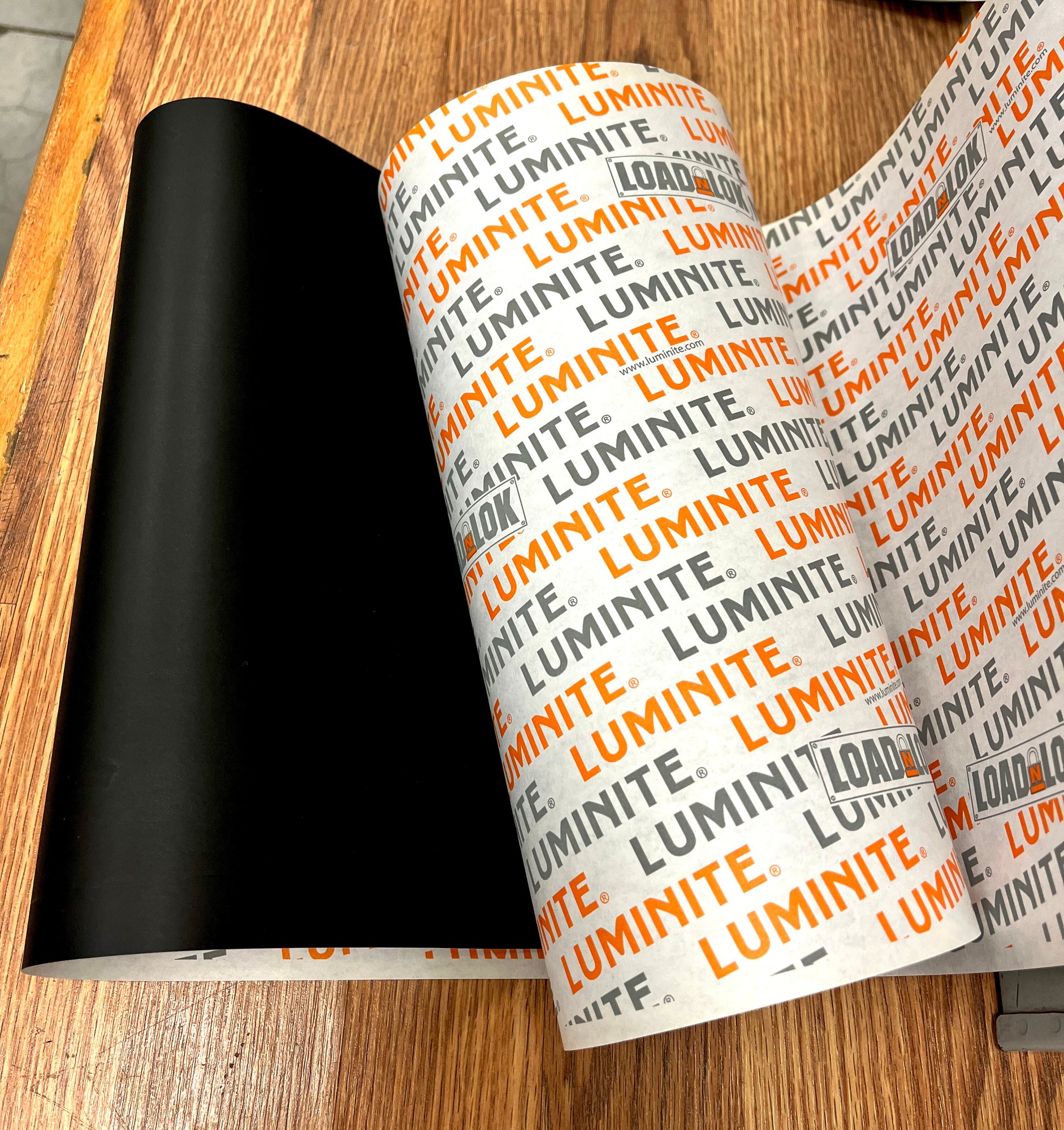
How Flexo Printing Works:
Flexo typically utilizes an elastomer or polymer image carrier such as sleeves, cylinders, and plates. The image carrier is engraved or imaged to create the design for the final desired product. Ink is transferred from the ink pan via an anilox roll onto the image carrier, where it is then printed onto the substrate.
Flexo printing is most commonly associated with uses in flexible packaging and labels, utilizing a variety of substrates including film, paper, foil and non-woven. Producing these products generally takes 3 steps:
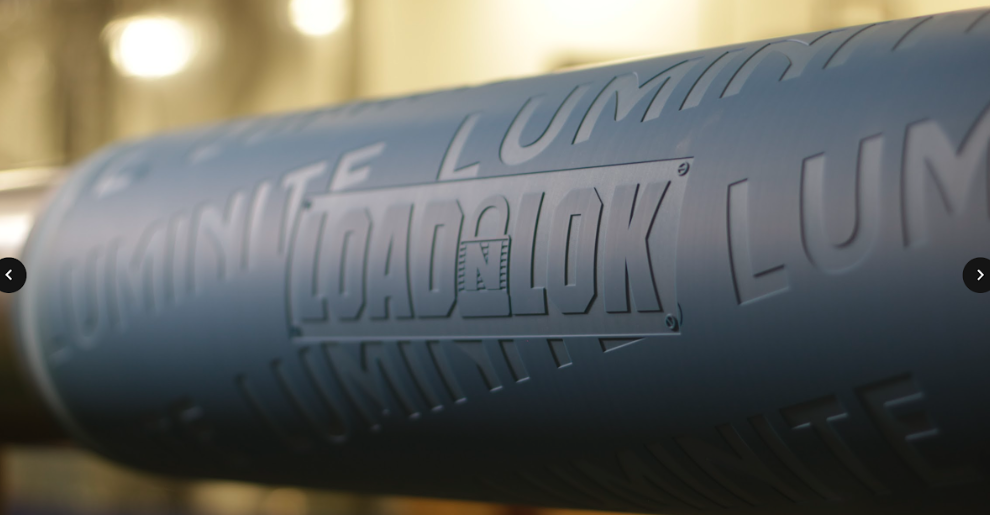
1. ARTWORK
The first step in flexographic printing is designing your artwork. Creating a design that fits the specifications needed to produce the final desired print can be challenging. Failure to thoroughly proof your artwork can result in costly mistakes.
Image carriers cannot be changed once they are produced.
When mounted to a printing cylinder, image carriers created flat stretch and distort your image. You can learn how to calculate and compensate for the distortion — or opt for In-The-Round, continuous print image carriers that are distortion-free.
2. WEB-FED SUBSTRATE MATERIALS
The flexographic printing press's rolling design allows continuous substrate materials (in roll form) to be fed through the machine.
This flexography feature allows for a continuous printing process to achieve high speeds, maintain accuracy, and efficiently produce large print runs.
3. THE FLEXOGRAPHIC PRINTING PRESS
- Unwind and Infeed — A roll of substrate is fed into the printing press. Tension must be kept taught to prevent slack which can cause wrinkling, misregistration, web breaks, and other print defects.
- Enclosed Doctor Blade Inking System — A continuous cycling pump fills the enclosed chamber with ink. The ink is transferred onto the anilox roll with any excess removed by the doctor blade. The ink cycles in and out of the enclosed system during printing.
- Inking Anilox Roller — The anilox roller contains microscopic cells, which carry a thin layer of ink from the inking system to the image carrier.
- Image Carrier and Impression Cylinder — The image carrier transfers the image to the substrate. The flexographic press pulls the substrate between the image carrier and the impression cylinder. Simultaneously, the impression cylinder holds exactly the right amount of pressure on the substrate for even ink distribution.
- Drying — The substrate winds through roller-less and plate-less sections to dry the ink. Depending on the number of colors used, the substrate might pass through multiple image carriers, impression cylinders, and drying sections in a single print run (one per color).
- Outfeed and Rewind — The final step on a flexographic printing press is the outfeed and rewind, where a substrate is rolled up again in preparation for a cutting die, which will separate individual prints.
How Litho Printing Works:
Litho printing is an offset process which uses a printing plate. The ink is first applied onto the printing plate and then transferred to a rubber blanket through multiple ink rolls, and finally applied to the substrate from the blanket.
This means the image is not printed directly onto the substrate from the plate.
What is the Difference Between Flexo & Litho Printing?
Both flexo and litho printing can produce reliable prints in very high volumes. They can produce quality product packaging, labels, and a wide variety of printed paper materials.
While lithographic printing might dominate some markets, flexo printing has increasingly gained popularity since the 1970s with the introduction of direct laser engraving.
COST:
Litho can accommodate foil stamping, spot gloss, embossing, and other embellishments, but these options also come at a higher cost.
Additionally, since the only way to print with litho is through an indirect pre-print, this guarantees an additional step in production and raises costs.
Both processes can be very cost-effective when printing large runs with basic needs.
With proper maintenance and storage, as well as an investment in durable image carrier materials, flexo image carriers can be reused many times before they need to be replaced.
SUBSTRATES:
Litho is generally limited to printing on smooth, flat surfaces as the image must be pressed onto the substrate.
Printing on corrugated substrates requires an additional step in production where the images are first printed onto linerboard, which is then attached to the corrugated substrate.
Flexo can print on both porous and non-porous surfaces, making it ideal for a wider variety of substrates, including coated linerboard and paper.
INKS:
Litho generally uses oil-based inks, and printing usually consists of the four process colors, each requiring a dedicated printing station.
Flexo also utilizes one image carrier per color and can use oil-based inks; it additionally accommodates printing with a wide variety of other inks — including water-based, solvent-based, and UV inks. Curable inks, such as UV, afford faster drying times. Faster drying can lead to faster production runs.
IMAGE QUALITY:
Flexo is noted for producing superior print with fine line and text detail.
Making the final decision whether to print using the flexo or litho process depends on the substrate, budget considerations, and many other production requirements.
How Digital Printing Works:
Digital printing presses function similarly to the printers we use at home. Unlike the other printing methods, digital printing does not require the creation of printing plates because a digital press uses electronic files to print images.
Digital printing is capable of rendering high resolution images. This method costs more per print than the other methods and moves more slowly, but without the need for printing plates, set up is less expensive.
This makes digital printing a great option for small volume printing, samples, or test marketing.
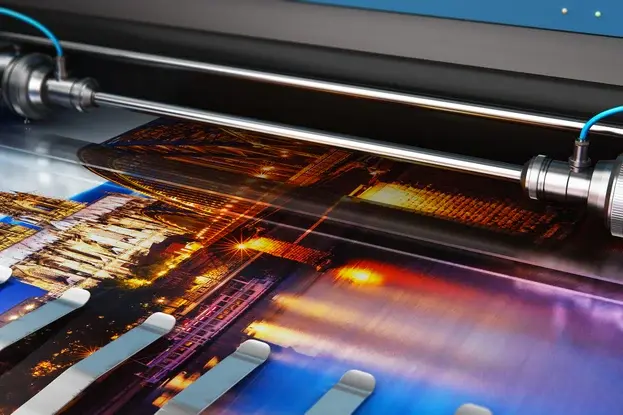
How Gravure Printing Works:
Gravure printing works by applying ink to a substrate with the use of a metal plate that is typically mounted onto a cylinder. This plate is often made of copper or chrome.
The image or text that is intended for printing is typically laser etched into the said metal plate, a process that often delivers high-quality and precise results with good repeatability.
What is the Difference Between Flexo & Gravure Printing?
COST AND LEAD TIME:
Gravure image carriers are typically much more expensive than Flexo, making the number of prints required to break even much higher. Gravure, however, has a longer press run time as the cylinders do not require as frequent changing as Flexo.
Gravure lead time is usually 3-4 times that of Flexo in the time it takes to manufacture the image carrier.
SUBSTRATES:
One of the limitations of gravure printing is that it is generally better suited for porous substrates. This is one of the reasons that Gravure is best suited for high-detail printing on applications such as magazine covers.
That isn’t the case with flexo printing, which can print on both porous and non-porous substrates, making the technology ideal for everything from film to paperboard.
INKS:
Another key differentiator is the range of inks Flexo can print with. Gravure is more limited in the inks it works with, often making Flexo the superior choice due to the ease of printing with a wider variety of inks.
Gravure requires much more ink per print, which can drive up the cost of printing.
ENVIRONMENTAL CONSIDERATIONS:
Traditionally, Gravure printing is associated with solvent-based inks, although advancements in water-based ink capabilities are emerging. As a result, Flexo is often viewed as the more environmentally friendly option.
Flexo generally has more options for VOC considerations, and the press operations are associated with more environmentally friendly practices.
QUALITY:
Gravure was once considered best for fine detail and tonal work, but Flexo technology is further enabling prints with higher resolution and detail as it evolves — enabling it to move into print jobs that were previously associated exclusively with Gravure.
How Offset Printing Works:
Similar to flexo, offset also uses a plate, but it works differently than flexo. Offset plates are usually made of metal, and the printing ink is transferred via the plate to a rubber piece of material (often this is called a "blanket") and then to the printing surface.
Offset is most commonly used to print on paper (think: newspapers and magazines), as a flat and smooth surface is required for printing.
.webp)
What is the Difference Between Flexo & Offset Printing?
INKS:
Flexo can operate with many more types of inks.
Offset generally works with inks that are oil-based along with using some water-based and UV-curable inks.
MAINTENANCE:
One thing to consider about offset is that the plates used in the process are susceptible to oxidation if they're not cared for properly. For this reason, extra maintenance is often necessary to ensure plate quality.
AFFORDABILITY:
Flexo image carriers are generally a bit cheaper to create and typically more durable than the plates used for offset — meaning they can be re-used a few times before replacement is necessary.
What's more, the wider range of inks that flexo works with (notably the faster drying times with low viscosity inks and UV inks) can accelerate print jobs and increase job profit.
CONVENIENCE:
As noted briefly above, offset printing can only be accomplished on a smooth, flat surface. Flexo, on the other hand, can print on a wide variety of substrates, making it a more convenient choice for many.
Combining this with Flexo’s ability to use many more types of ink and the ease of printing more large-scale tasks, it is often hailed as the superior choice.
So what process is right for you? It largely depends on the job, substrate, and various other factors of the job you're printing.
What is Screen Printing?
Screen printing has evolved from the two color machine presses utilized in the 1960s for various print applications. The old presses featured a long dryer between print stations and rigid wire screens that contained photographic emulsion.
Since the 1960s, the screen printing process has evolved greatly with the improvement of technology and materials.
Label and Narrow Web magazine explains the modern process of screen printing:
“Screens, which come in a variety of meshes, are covered by chemical emulsions, which are the proprietary products of the manufacturers. To prepare a screen for use, a film containing a positive image is placed on the screen and exposed to light.
"The screen is then washed with water, which removes unexposed emulsion and opens the mesh below the image areas. In exposed areas the emulsion fuses together, closing all mesh openings to prohibit ink flow.”
Though screen printing is standard, there are two types of screen printing — flat and rotary — that differ slightly in process.
FLAT SCREEN PRINTING
During flat screen printing, the exposed screen is arranged over the top of the chosen substrate. The ink is then deposited in front of a squeegee. The squeegee then moves over the screen, forcing the ink through the mesh and creating a print.
ROTARY SCREEN PRINTING
The rotary screen process differs slightly. Rather than the squeegee moving atop the screen, it is fixed inside of the screen. The squeegee and screen are mounted ITR, and ink is introduced.
When the mounted cylinder rotates, the ink is forced through the mesh via the squeegee. The substrate moves outside the screen and receives the ink, producing a print.
Flexo Printing vs Screen Printing
SUBSTRATES:
The substrates available for screen printing, specifically rotary screen printing, are limited compared to flexo. The most common substrates used for screen printing include:
- Textile
- Sign board
- Film
- Paper
Though flexo is not a common choice for printing on textiles, it does support a wider variety of substrates and executes detailed prints.
INKS:
In general, most inks used for rotary screen printing are UV-curable, especially for use in narrow web applications. There are some projects, however, that require solvent-based inks, which can be used.
When it comes to color, white ink is the most popular in the screen printing market.
Flexo utilizes a wider variety of inks. A full guide to the inks used in flexo printing, and the considerations based on application, can be found here.
SPEED:
Due to the high number of jobs that utilize UV-curable inks, print speed largely depends on the ink and more, specifically the amount of time the ink requires for curing.
Because of this, print run speeds are slower than that of flexo.
Corrugated Printing Considerations:
Today's advanced technologies and materials have revolutionized printing on corrugated packaging materials. With modern printing technologies and the ever-increasing capabilities of flexo, brands can simultaneously use corrugated product boxes to increase product visibility and promote a brand’s awareness, in addition to benefiting from the material's lightweight durability which is ideal for shipping.
The variety of available processes and materials have created several methods for printing on corrugated material, including flexography (flexo), offset lithography (litho), screen printing, and digital printing. Due to its versatility, flexographic printing has become one of the most commonly utilized.
We have a complete guide to Flexo Printing on Corrugated!
Four Options for Printing on Corrugated Substrates
1. OFFSET LITHOGRAPHY (LITHO LAMINATION)
Not actually a direct printing method, lithography pre prints images onto linerboard, which is then attached to the corrugated substrate. While this is an option for all printing methods listed, this is the only way to print on corrugated with litho, which guarantees an additional step in production.
This method easily accommodates foil stamping, spot gloss, embossing, and other embellishments and renders high-resolution images.
Lithography's nearly limitless options come at a premium. The set up, added embellishments, and pre-printing method all increase costs.
2. SCREEN PRINTING
During the screen printing process, a squeegee forces ink through a screen, depositing color onto the substrate. Stencils (masks) shield negative space from ink and allow ink to pass through onto colored areas.
A stencil is made for each separate color, and each color is applied separately. It is a time-consuming process that is often done by hand.
It produces richly colored images but it is most suitable for small-volume prints.
3. DIGITAL PRINTING
Digital printing presses function similarly to the printers we use at home. Unlike the other printing methods, digital printing does not require the creation of printing plates because a digital press uses electronic files to print images.
Digital printing is capable of rendering high-resolution images. This method costs more per print than the other methods and moves more slowly, but without the need for printing plates, set up is less expensive.
This makes digital printing a great option for small-volume printing, samples, or test marketing.
4. FLEXOGRAPHY (FLEXO)
By far the most popular choice for printing on corrugated substrates, flexography uses an inked image carrier to transfer graphics onto a substrate. The process is gentle enough for corrugated substrates and can still achieve vibrant graphics on the final product.
Since flexography requires printing image carriers (one per color), there is some up-front cost associated with set up. Once the printing image carriers are ready, however, flexography is a cost-effective and high-speed method for printing large-volume orders with attractive graphics.
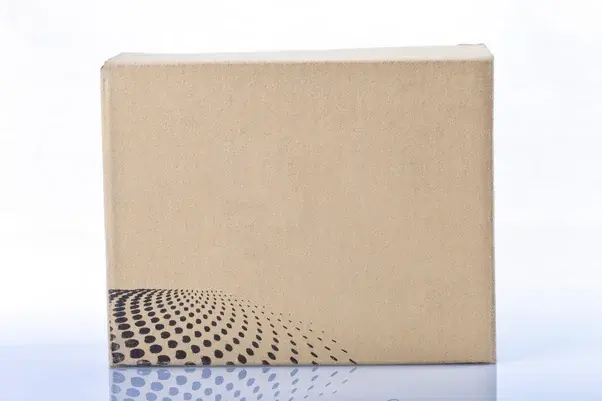
Flexo Hybrid Presses:
The commercial printing industry has recently seen the popularity of hybrid presses grow. Consumer products require more intricate prints and durable final products, forcing printers to adjust their capabilities to meet demands.
This has resulted in many printers opting for hybrid presses, which deliver more of the “pros” of each of the above printing methods, without sacrificing quality or efficiency.
DIGITAL FLEXO HYBRID PRESSES:
One of the main reasons printers opt for digital flexo hybrid presses is that it allows the flexographic printing process to better accomplish shorter runs, without sacrificing the quality of a final flexo print.
Hybrid presses enable full-color digital inkjet technology to be utilized with an existing flexo press. Brand new digital presses that feature flexo printing stations are also available.
Ready to Get Started with Flexo?
If you’re ready to get started printing with flexography, contact the experts at Luminite today. Our team is eager to help manufacture and supply quality flexographic image carriers that are perfect for your project requirements.
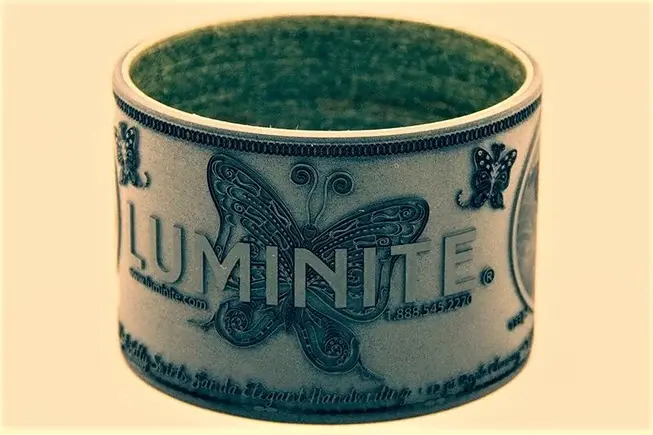