The Flexography Process: A Look at Luminite Production
- Receiving / Incoming Inspection
- Base Preparation
- Rubber Wrap
- Autoclave / Vulcanization
- Rough Grind
- Trim
- Finish Grind
- Polishing
- Laser Engraving
- Print Proof
- Final Clean-up
- Final Inspection
- Shipping
STEP 1: RECEIVING / INCOMING INSPECTION
All new and used sleeves, integral shafts, demounts, and narrow web units that come into Luminite are carefully inspected to check that the specifications on bearing journals, bores, gears, etc. are within tolerance before going into production.
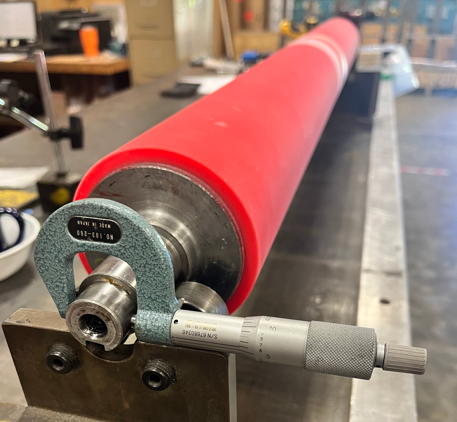
Anything found out of tolerance is presented to the customer for repair or replacement options.
Luminite’s internal engineering staff is well-equipped to provide a solution to any out-of-tolerance condition.
STEP 2: BASE PREPARATION
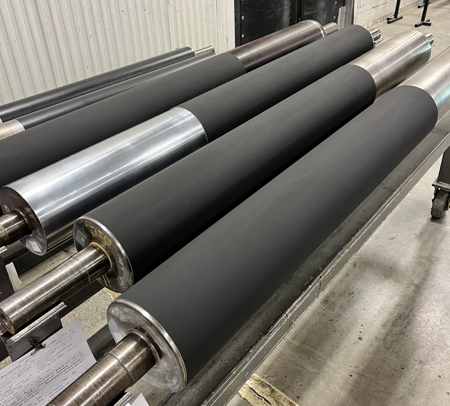
The bases are then carefully cleaned and prepared to begin the upcoming process.
STEP 3: RUBBER WRAP
Primers and adhesives are then carefully applied to the units maintaining controlled thickness specifications. There can be anywhere from 1 to 3 applications depending on the elastomer being applied. Specified dry times between coats and before elastomer application are carefully monitored to ensure bonding integrity.
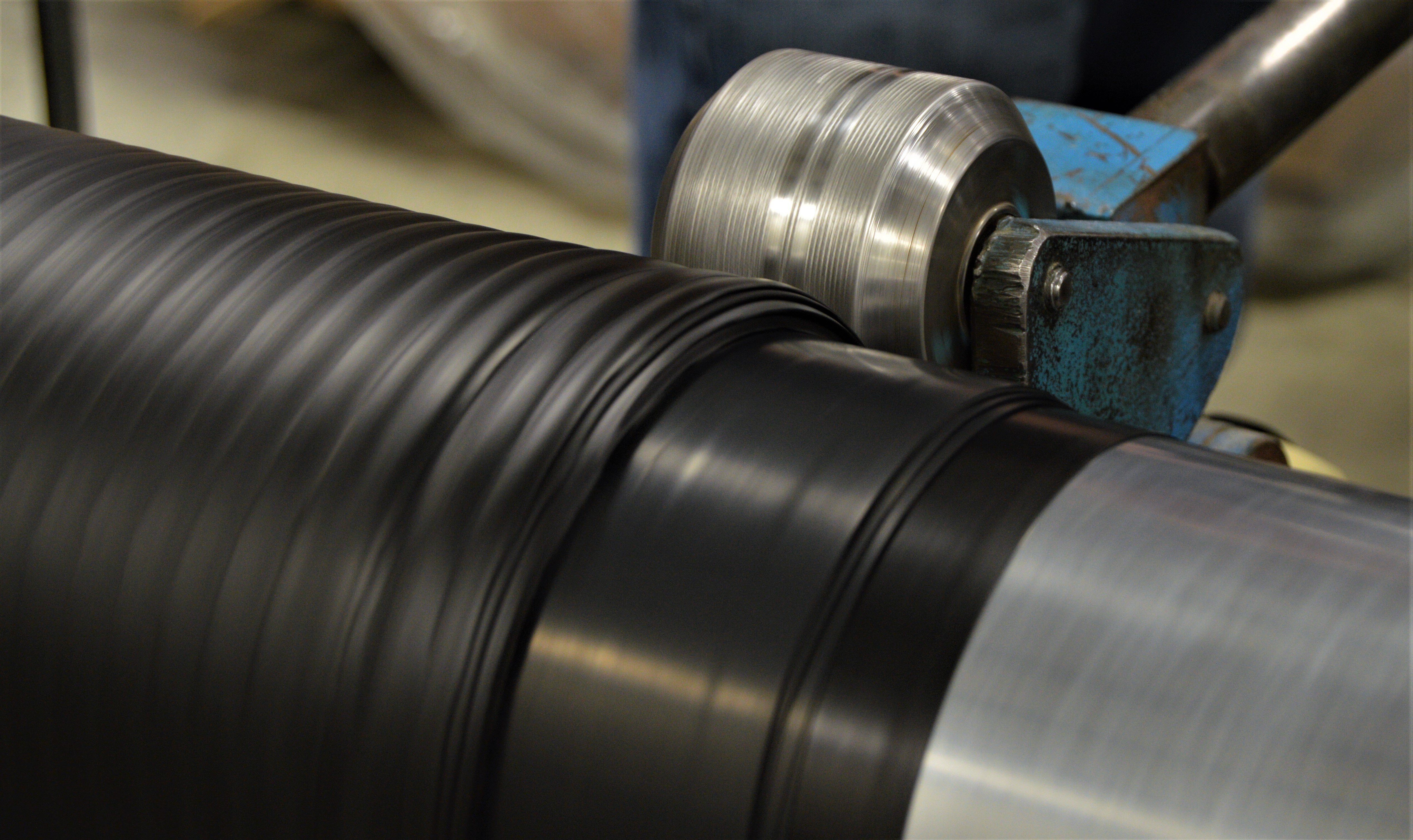
The elastomer is applied to the unit using specialized elastomer strip-building equipment. Rubber strips are fed into a machine where the rubber is heated and extruded through multiple strainer screens to ensure no contaminants are in the final product.
STEP 4: AUTOCLAVE / VULCANIZATION
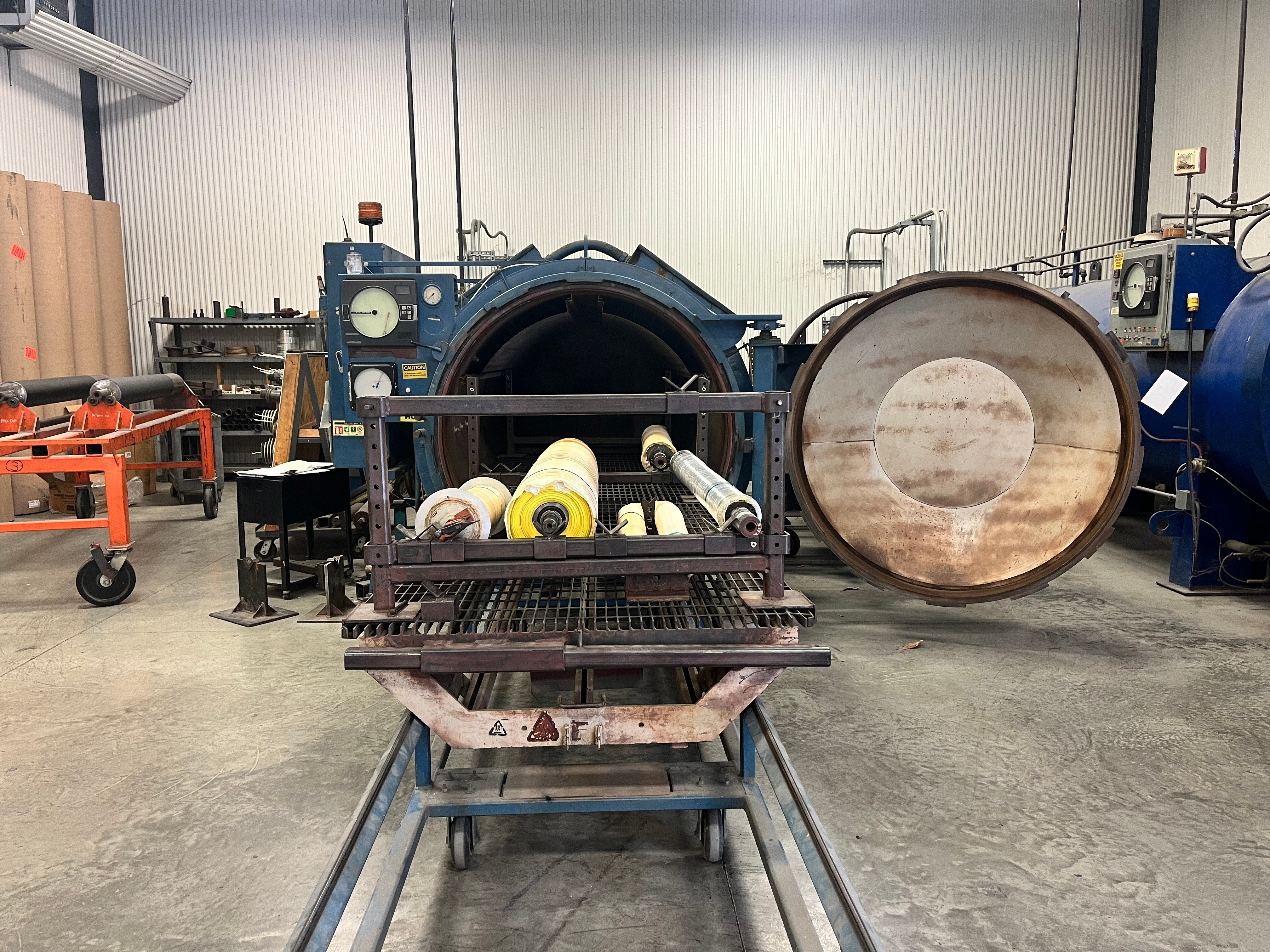
The wrapped image carrier is placed in the dry-heat autoclave for curing. During this process, all seams are removed from the surface of the sleeve. At Luminite, we opt for dry heat to protect moisture from degrading the cylinders. Most rubbers are cured for 24 hours before the next steps can begin.
STEP 5: ROUGH GRIND
After the curing process is complete and rollers are cooled to ambient temperature, the vulcanizing tape is removed and rollers are rough ground or thermo-cut to a specified amount over the final finish diameter. This is dependent on the elastomer and stock removal method that was used.
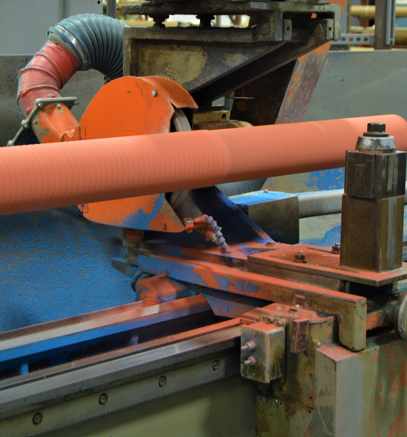
The hardness of the rubber is initially verified to be in the specification at this point in the process.
STEP 6: TRIM
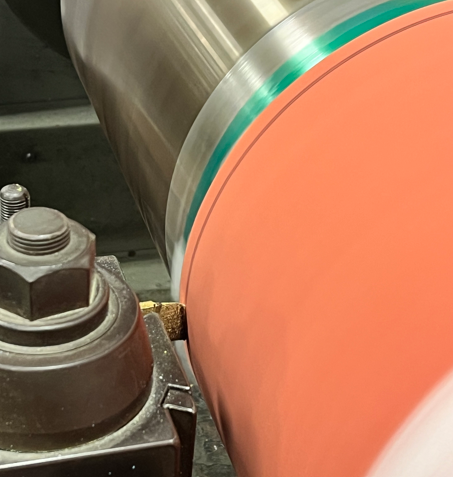
The goal of this step is to remove any excess rubber from the image carrier. Additionally, the product is staged for finish grinding.
STEP 7: FINISH GRIND
There is a 24- to 48-hour rubber stabilization period before the final grinding.
During the finish grinding process, special attention is given to temperature control to ensure dimensional stability. We use a variety of precision tooling and specialized hardware to precisely grind off the same journal, bearing or bore that the rollers run off of on press.
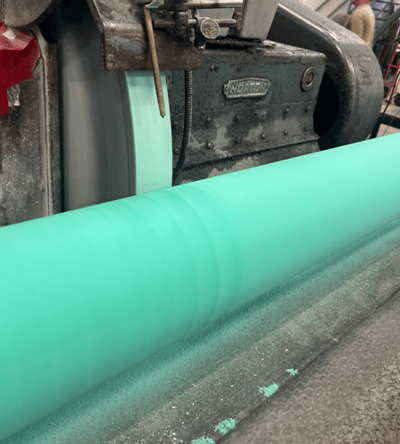
This helps to keep the most concentric rubber surface to impression roller contact possible.
STEP 8: POLISH
Once the roller is at the specified finish diameter the surface is micro-polished for a smooth consistent finish, roller after roller.
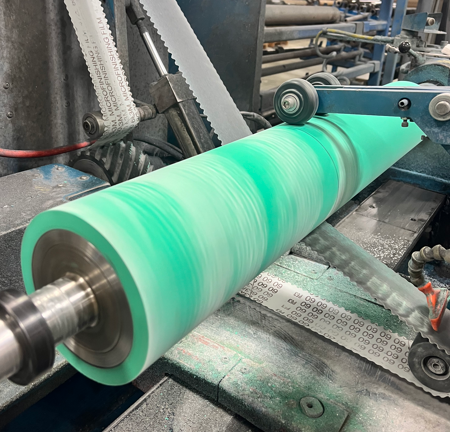
QC department monitors RA recording off the polisher on all jobs to ensure the rubber surface finishes are consistent time after time.
STEP 9: LASER ENGRAVING
In the laser engraving department, we house three digital direct laser engraving systems. They use both CO2 and Yag laser technology that can work either individually or simultaneously during the engraving process for flexographic printing.
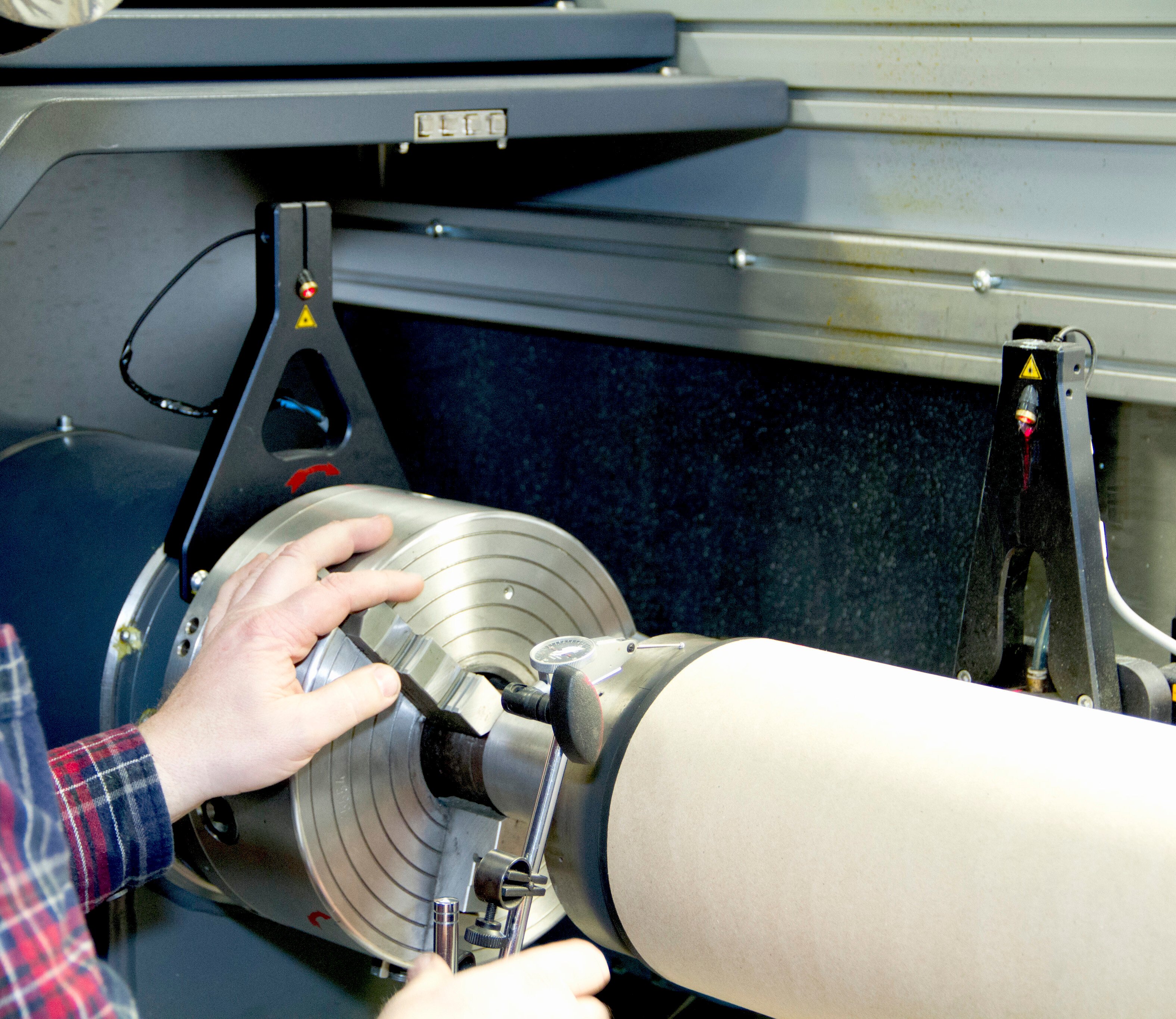
This gives Luminite the full spectrum of ITR engraving possibilities.
STEP 10: PRINT PROOF
After the image is engraved into the roller and cleaned we start our inspection process. The first stage is to make an actual image proof of the roller.
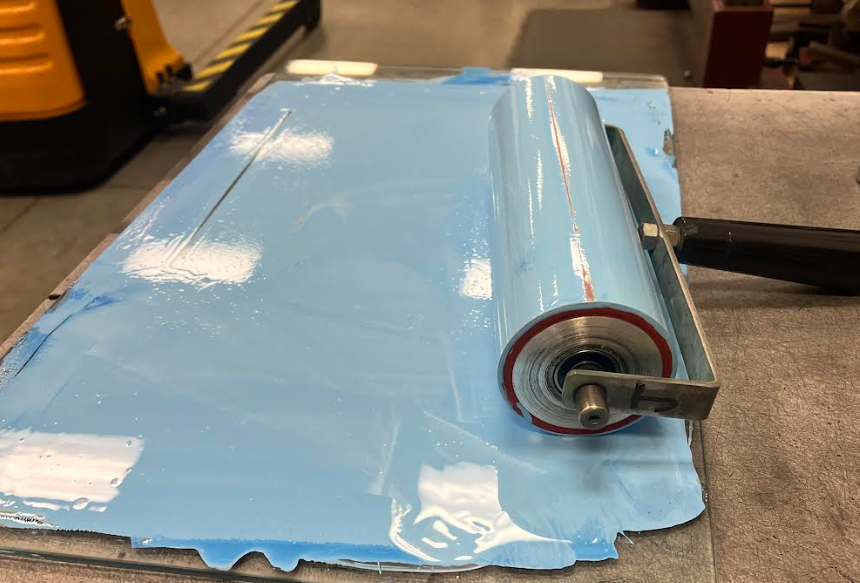
This step verifies the concentricity of the ground surface, that the roller is free of any low spots or surface defects, all engraved elements are printed and provide sharp transfer.
STEP 11: FINAL CLEAN-UP
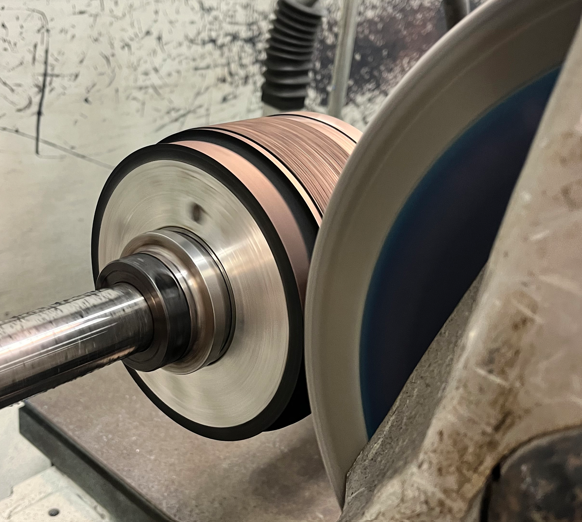
We do a final clean-up of the roller. This removes any rubber not used for printing and may be left on the roller after engraving.
STEP 12: FINAL INSPECTION
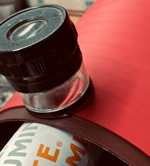
Design, width, depth, and other flexographic printing defects are all checked for during this phase.
STEP 13: SHIPPING
When it comes to shipping the roller, it is important to focus on care and protective packaging.
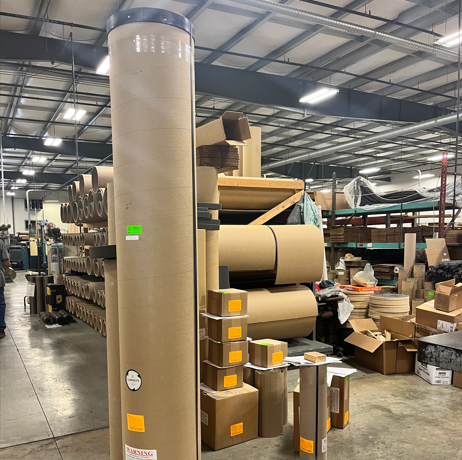
We use a variety of:
- Protective wraps
- End shock protection
- Corrugated tubes
- Boxes
- Wooden & steel crates
Print Industry Standards
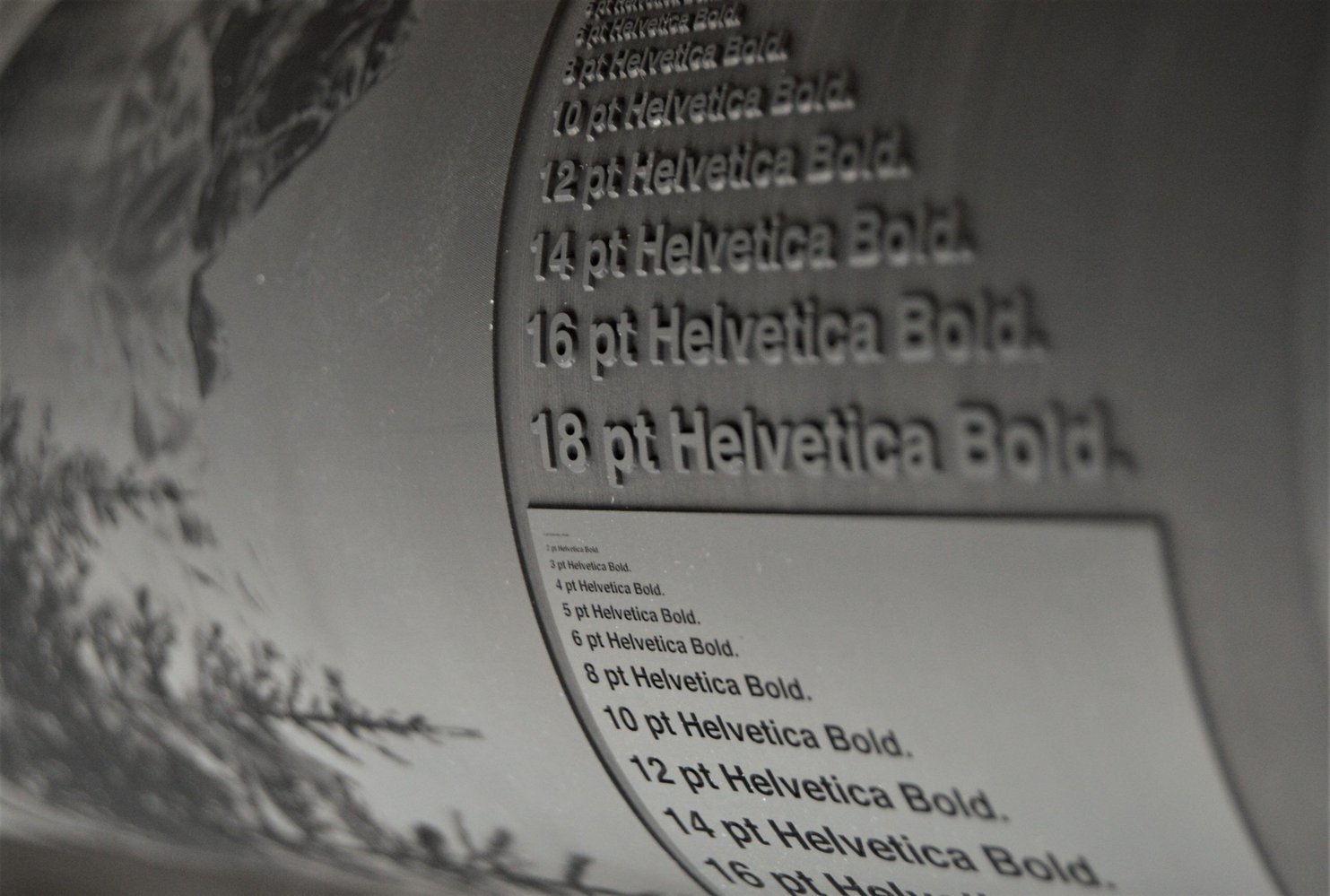
Our staff at Luminite recognize the many standards the printing industry has to meet. We find this requires regular monitoring to make note of adjustments. Likewise, efforts must change to keep up with the standards as they are presented.
A prime example of how standards from various industries can overlap with commercial printing is FDA regulations. The Food and Drug Administration has stringent regulations on anything that will comprise a part of food or drug packaging.
The FDA’s primary goal is consumer protection through safety. As such, they provide printing industry safety standards for any product that will come into contact with a food or drug product. Unlike ISO standards, these standards function with the full force of law. Due diligence must be paid to ensure you are following all FDA-compliant materials standards. Relevant FDA standards regulate many materials used for products within the FDA’s review:
- Ink. Strict adherence to FDA guidelines is required for ink that may come into contact with food or medicine to prevent contamination.
- Packaging materials. The FDA has strict requirements for food-grade and medical-grade plastics to ensure that packaging doesn’t deteriorate the reliability of a perishable product or cause harmful reactions like leaching.
- Medical- and food-grade metals and plastics. Materials for equipment used in the food or medical industry are also regulated by the FDA, and plastic or steel being printed on for medical equipment or food preparation use must also meet FDA standards.
Your product should speak for itself, and consistency and quality prints every time are important. For commercial printing, internal standards can make you a more valuable partner for contracts. If someone comes to you with very specific colors that are quintessential to their brand, you need to produce that exact color every time. Setting standards internally is an important way to ensure that quality.